Unlocking the Full Potential of the Best Prototype Machine with Detailed Specifications and Usage Guide
In today's fast-paced technological landscape, the demand for rapid prototyping has never been greater, making the prototype machine an essential tool for engineers, designers, and innovators alike. This comprehensive guide aims to unlock the full potential of the best prototype machines available on the market by providing detailed specifications and usage insights. Whether you're an industry veteran or a newcomer looking to enhance your workflow, understanding the capabilities and functionalities of these machines is crucial. From 3D printing to CNC machining, prototype machines offer unparalleled versatility in transforming ideas into tangible products. In this blog, we will delve into the various types of prototype machines, their unique features, and best practices for optimizing their use, ensuring you can make informed decisions and elevate your prototyping processes to new heights.
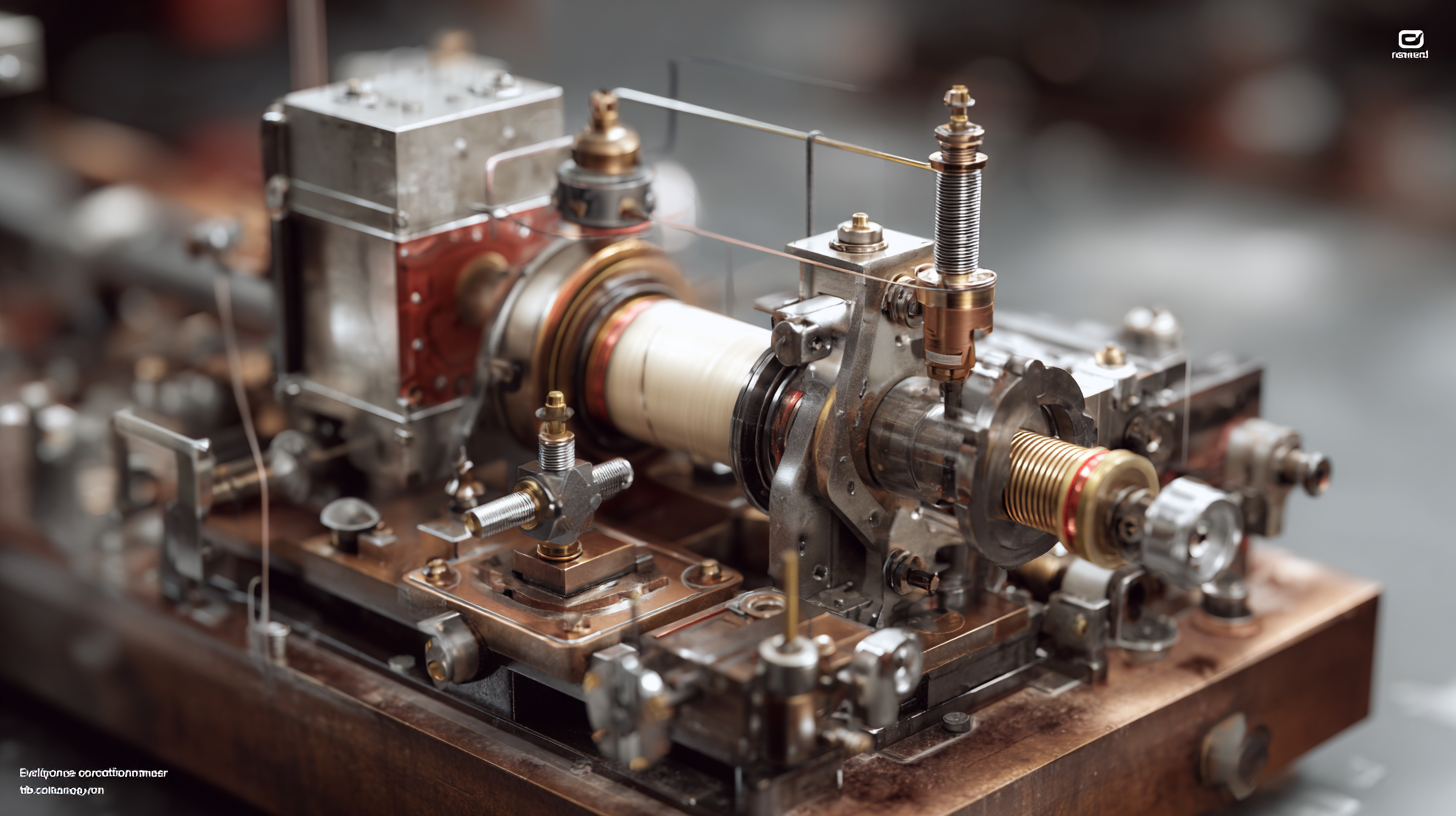
Exploring the Key Features of the Best Prototype Machine for Enhanced Productivity
The best prototype machine is designed to transform concepts into reality with remarkable precision and efficiency. One of the key features that sets this machine apart is its advanced CAD integration, allowing users to seamlessly import designs and make real-time adjustments. This capability not only streamlines the prototyping process but also enhances collaboration among teams, ensuring that everyone is on the same page throughout development. The intuitive software interface further empowers users, making it easy to navigate complex functions without extensive technical knowledge.
Another significant aspect of the best prototype machine is its versatility in materials handling. It supports a wide range of materials, from plastics to metals, enabling creators to explore diverse possibilities. This adaptability opens up new avenues for innovation, allowing businesses to test various prototypes without the limitations usually associated with traditional machines. Additionally, the precision engineering of this machinery leads to higher quality outputs, reducing the time spent on revisions and adjustments. Overall, these features contribute to enhanced productivity, helping teams bring their visions to life more efficiently and effectively.
Comprehensive Specifications: Understanding Size, Weight, and Power Requirements
In the world of modern technology, understanding the specifications of equipment plays a crucial role in maximizing their potential. When it comes to prototypes, key metrics such as size, weight, and power requirements are paramount. For instance, a recent review highlighted how a well-designed prototype can achieve impressive functionality while maintaining a lightweight structure. This innovation is reminiscent of products that combine a powerful motor with a lightweight design, ultimately enhancing user experience and performance.
Taking a closer look at specifications, the dimensions and weight of devices significantly impact their usability. For example, flagship smartphones are developing increasingly compact profiles, with average weights around 221 grams and dimensions that fit comfortably in hand. Such metrics are not merely aesthetic; they contribute to the overall portability and efficiency of the device. Additionally, power requirements have evolved, allowing these devices to operate effectively without draining energy excessively—paving the way for sustained performance without compromising on durability and convenience.
Therefore, aspiring designers and engineers must prioritize these specifications in their prototypes. By focusing on the right balance of size, weight, and power, they can unlock the full potential of their innovations, setting new standards in the industry and providing users with top-tier performance in a manageable form factor.
Step-by-Step Guide: Setting Up Your Prototype Machine for Optimal Performance
When it comes to setting up your prototype machine for optimal performance, a meticulous approach is essential. Start by choosing a suitable location; ensure that the workspace is clean, well-ventilated, and has access to necessary utilities. Position the machine on a stable, flat surface to prevent any wobbling during operations. This foundation will significantly contribute to the machine's accuracy and longevity.
Next, refer to the detailed specifications provided in the user manual for proper assembly. Follow each step methodically to avoid missing any critical components. A common tip is to keep all tools organized and within reach during the setup process, which will save time and reduce frustration. After assembly, it’s crucial to conduct a preliminary check. Power on the machine and run diagnostic tests to verify that all systems are functioning correctly. Any unusual sounds or malfunctions should be addressed immediately to prevent complications in later stages.
Finally, take the time to familiarize yourself with the software that accompanies your prototype machine. Understanding its features and capabilities can enhance your workflow and efficiency. Consider creating a checklist of essential settings and adjustments you might need frequently. This proactive step can help streamline your operations and allow you to unlock the machine's full potential.
Tips for Maintenance and Troubleshooting Common Issues in Prototype Machines
Maintaining a prototype machine is crucial to ensuring its optimal performance and longevity. Regular maintenance checks can prevent minor issues from escalating into significant problems. Start by routinely inspecting all moving parts, including gears and belts, for signs of wear and tear. Lubrication should be applied according to the manufacturer’s specifications, as dry components can lead to increased friction and potential breakdowns. Additionally, keeping the machine clean from dust and debris will help in maintaining the precision and accuracy of the prototypes produced.
Troubleshooting common issues is another essential aspect of managing prototype machines. If you encounter inconsistent outputs, first check the calibration settings, as improper adjustments can lead to variations in product quality. In cases of unexpected shutdowns or performance lags, it’s advisable to review the electrical connections and ensure that power supply is stable. Regularly updating the software and firmware can also resolve many operational glitches. By following these maintenance and troubleshooting tips, users can efficiently enhance the functionality of their prototype machines while minimizing downtime.
Maximizing Efficiency: Best Practices for Utilizing Your Prototype Machine Effectively
When it comes to maximizing the efficiency of your prototype machine, understanding best practices can make a significant difference. Start by ensuring that you are familiar with the machine's detailed specifications. Knowing its capabilities and limitations allows you to harness its full potential effectively. Make it a habit to consult the user manual regularly and stay updated with any software or firmware updates that may enhance performance.
Another key aspect of efficient utilization is maintaining an organized workspace. Ensure that your materials and tools are within easy reach, minimizing downtime during the prototyping process. Regularly calibrating the machine and conducting maintenance checks can also prevent potential setbacks. Additionally, consider training sessions or workshops that focus on advanced techniques for using your prototype machine, which can lead to better results and innovation in your projects. By implementing these best practices, you can significantly enhance the productivity and outcomes of your prototyping endeavors.