Unveiling the Specifications: The Ultimate Guide to the Best CNC Lathe Machine for Global Buyers
As the manufacturing landscape evolves, the demand for precision engineering tools such as the CNC lathe machine is surging. According to a recent market analysis, the global CNC lathe machine market is projected to reach USD 5.56 billion by 2025, growing at a CAGR of 6.2% from 2020. This growth is driven by advancements in automation and the increasing need for high-precision components across various industries, including aerospace, automotive, and electronics. As manufacturers seek to optimize production processes and enhance product quality, understanding the specifications and capabilities of CNC lathe machines becomes crucial. In this ultimate guide, we will unveil the essential features, performance metrics, and innovative trends shaping the best CNC lathe machines available to global buyers in 2025, ensuring you are well-equipped to make informed purchasing decisions in this competitive market.
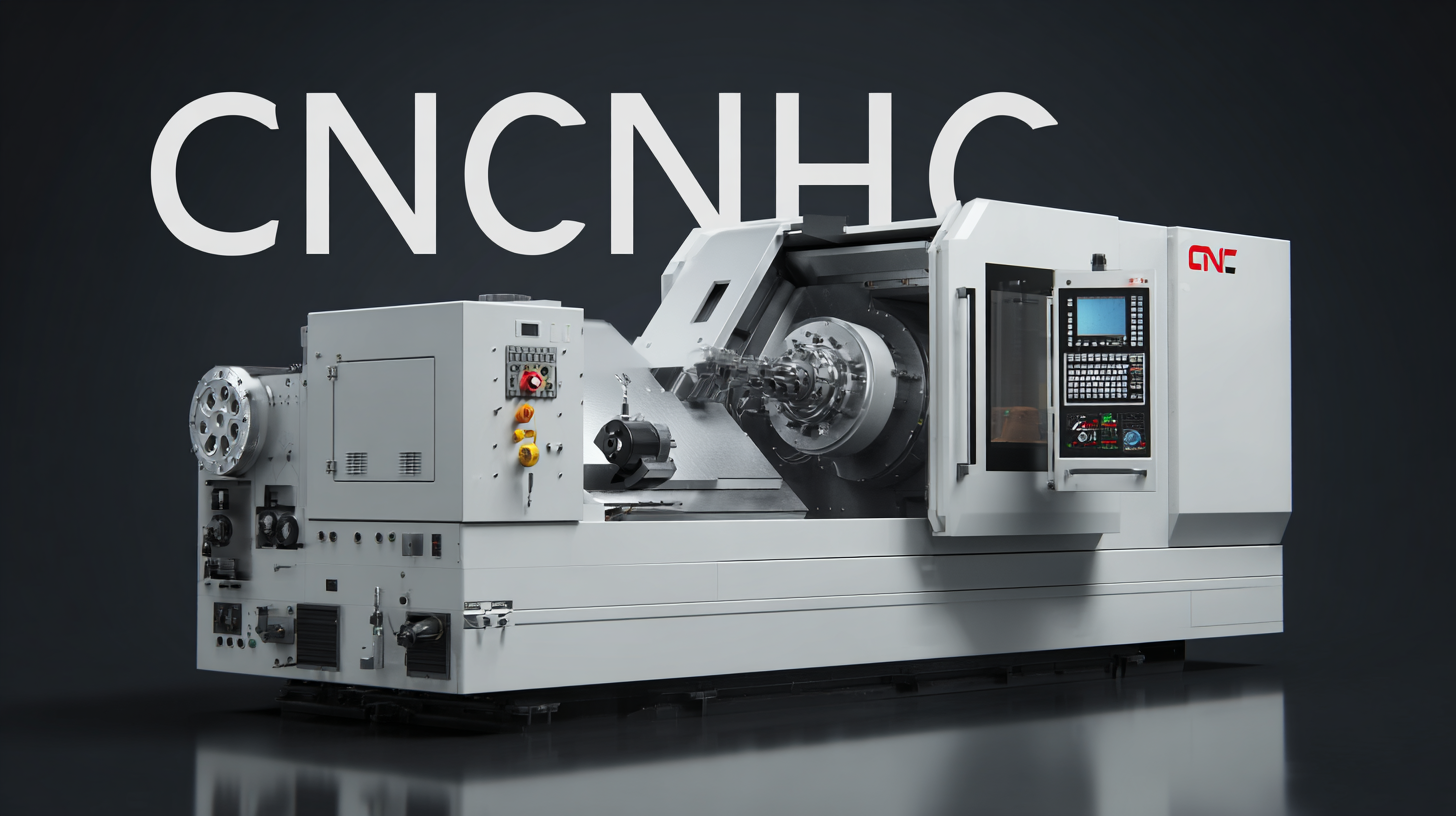
Understanding CNC Lathe Machines: Key Features and Technologies
CNC lathe machines play a vital role in modern manufacturing, offering precision and efficiency that are essential for producing high-quality components. Understanding the key features and technologies of these machines is crucial for global buyers looking to invest in the best options for their operations. Central to the allure of CNC lathe machines are their capabilities for automation, which significantly enhance production rates and reduce human errors. Moreover, advancements in multi-axis machining and high-precision capabilities are driving increased demand across various industries.
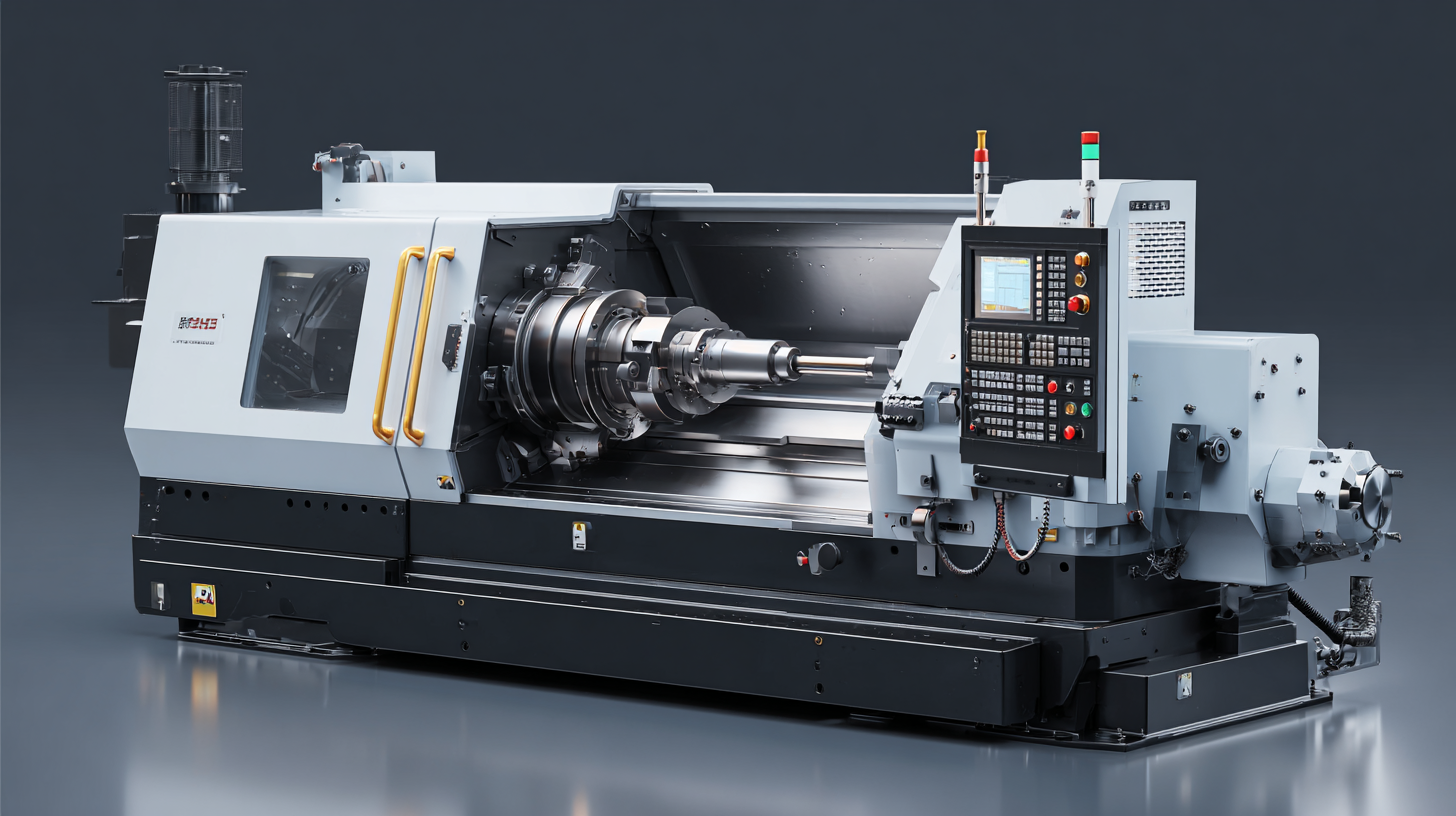
In recent years, the market for CNC machines has witnessed unprecedented growth, projected to reach values of $195.59 billion by 2032. This surge is largely fueled by innovations in technology, particularly the integration of artificial intelligence and the Internet of Things (IoT), which are reshaping the landscape of manufacturing. Manufacturers are increasingly seeking high-precision solutions, and CNC lathe machines equipped with the latest technologies not only meet these demands but also set new benchmarks for accuracy and reliability. As the industry continues to evolve, understanding these key features will be essential for making informed purchasing decisions.
Evaluating Manufacturer Credibility: What to Look For
When selecting a CNC lathe machine for your business, evaluating the manufacturer’s credibility is crucial. A reliable manufacturer should have a robust history in the industry, showcasing years of experience and consistent innovation. Look for companies that have received industry awards or certifications, as these accolades often reflect their commitment to quality and excellence in manufacturing.
Tips: Always check customer testimonials and case studies on the manufacturer’s website or independent review sites. Positive feedback from existing clients can provide insights into the reliability of machines and the level of customer support offered. Additionally, inquire about after-sales service and warranty policies to ensure that you have support for any potential issues post-purchase.
Another aspect to consider is whether the manufacturer follows international standards and practices. Compliance with ISO or similar quality management systems ensures that their products meet specific criteria of quality and safety. This not only reinforces the manufacturer’s credibility but also assures you that the CNC lathe machine you purchase will perform reliably over time.
Tips: Request details about the production process and quality control measures the manufacturer employs. A transparent production process can significantly boost your confidence in their products, knowing that they prioritize quality at every stage of manufacturing.
Unveiling the Specifications: The Ultimate Guide to the Best CNC Lathe Machine for Global Buyers - Evaluating Manufacturer Credibility: What to Look For
Specification | Parameter | Description |
---|---|---|
Max Swing Over Bed | 350 mm | The maximum diameter of the workpiece that can be swung over the bed. |
Max Turning Length | 1000 mm | The longest length of the workpiece that the lathe can handle. |
Spindle Speed | 6000 RPM | The maximum speed at which the spindle rotates. |
Tool Holder Type | ISO 7379 | Standard type for quick tool change. |
Control System | CNC Controller | Computer numerical control system for precise operations. |
Power Supply | 220V/380V | Input voltage for standard operation. |
Weight | 1000 kg | Total machine weight, affecting stability. |
Top CNC Lathe Brands: A Comprehensive Comparison
When it comes to choosing the best CNC lathe machines, global buyers must navigate a landscape dotted with numerous top brands that offer varying features and capabilities. According to a recent report by Market Research Future, the global CNC lathe machine market is expected to grow at a CAGR of 5.3% between 2021 and 2026, driven by the increasing demand for automation and precision in manufacturing. This growth has propelled leading CNC lathe brands, such as Haas Automation, Mazak, and DMG Mori, to invest heavily in R&D, ensuring that their machines remain at the forefront of technology.
Haas Automation, renowned for its user-friendly interface and robust build quality, remains a favorite among both small and large-scale manufacturers. Their machines are designed for ease of operation, and they often rank highly in customer satisfaction surveys, with a reported 90% satisfaction rate in a 2022 industry study. On the other hand, Mazak has carved a niche for itself with advanced multi-tasking capabilities, allowing for simultaneous machining processes, which is crucial for efficient production. According to a survey by TechSci Research, Mazak’s market share in North America alone stood at 20% in 2023, underscoring its dominance in the CNC lathe sector. Meanwhile, DMG Mori excels in high-precision machining with their innovative designs, making them a preferred choice for sectors demanding utmost accuracy, such as aerospace and medical device manufacturing.
Comparison of CNC Lathe Machine Features
Common Types of CNC Lathes and Their Best Use Cases
When it comes to CNC lathes, understanding the various types and their ideal use cases is crucial for making an informed purchasing decision. The most common types of CNC lathes include flatbed lathes, slant bed lathes, and multi-axis lathes. Flatbed lathes are known for their straightforward design and versatility, making them suitable for a wide range of materials and applications. They excel in producing detailed components for industries like automotive and aerospace, where precision is paramount.
Slant bed lathes, on the other hand, are designed for efficient chip removal and enhanced processing stability. Their angled design facilitates easier access to the workpiece, making them a top choice for high-volume production environments. Industries that require repetitive machining tasks find slant bed lathes beneficial due to their speed and efficiency.
Multi-axis lathes represent the pinnacle of CNC lathe technology, offering advanced capabilities for complex parts and intricate designs. These machines are ideal for specialized sectors such as medical device manufacturing and custom automotive components, where precision and versatility are essential.
Practical Solutions for Sourcing and Maintenance of CNC Lathes
When it comes to sourcing CNC lathe machines, understanding their maintenance requirements is crucial for maximizing operational efficiency and minimizing downtime. Recent advancements in predictive maintenance technologies have highlighted the importance of monitoring performance metrics actively. According to industry reports, companies that implement predictive maintenance strategies can potentially reduce their maintenance costs by up to 30% while increasing machine uptime by as much as 20%. This underscores the value of investing in machines equipped with real-time monitoring capabilities, allowing users to anticipate issues before they escalate.
Moreover, lessons learned from various EU-funded H2020 research projects emphasize the need for continuous development in maintenance technologies. These projects indicate that integrating machine learning algorithms can significantly enhance the accuracy of maintenance predictions. By systematically analyzing data collected from CNC lathes, manufacturers can create tailored maintenance schedules that not only ensure the longevity of their machines but also optimize their overall production processes. Adopting such practical solutions for sourcing and maintenance will empower global buyers to make informed decisions, ultimately elevating their operational standards in a competitive market.