Ultimate Guide to Selecting the Best CNC Lathe Machine for Your Business Needs
In an era where precision and efficiency are paramount in manufacturing, the CNC lathe machine has emerged as a cornerstone technology in machining processes. According to a recent report by MarketsandMarkets, the global CNC machine market is projected to reach USD 100 billion by 2025, with CNC lathes accounting for a significant share due to their versatility and automation capabilities. As businesses strive to enhance productivity and reduce operational costs, selecting the right CNC lathe machine becomes crucial. The growing demand for customized and complex parts across industries such as aerospace, automotive, and medical devices further emphasizes the need for advanced machining solutions.
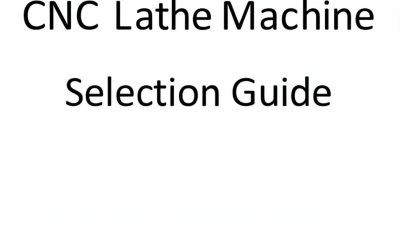
This ultimate guide aims to navigate the essential factors to consider when choosing the best CNC lathe machine tailored to your business needs, ensuring you make informed decisions that align with technological advancements and market trends.
Understanding CNC Lathe Machines: Key Features and Specifications to Consider
When selecting the best CNC lathe machine for your business needs, it is crucial to understand the key features and specifications that can significantly impact your production efficiency and overall costs. One major aspect to consider is the energy efficiency of the machines.
Advanced CNC systems are now designed to help reduce CO2 emissions, making them a critical factor for companies looking to optimize their processes sustainably. By investing in energy-efficient models, businesses not only contribute to environmental preservation but also enjoy cost savings in their operations.
Another important consideration is the ability to retrofit existing machines. Rather than prematurely scrapping old equipment, companies can explore options to retrofitting, which allows for the continuation of existing machinery with enhanced features. This approach not only extends the lifespan of valuable tools but also enables the incorporation of modern capabilities without the high costs typically associated with brand-new machines. As the CNC machine market is projected to grow significantly, keeping worn parts operational through retrofitting will be increasingly vital for companies aiming to remain competitive and innovative in their production methodologies.
Emerging Technologies in CNC Lathe Machines: Trends Shaping the Industry by 2025
The CNC lathe machine industry is witnessing a transformative phase driven by emerging technologies and increasing market demand. As businesses seek high-precision solutions, innovations in AI and robotics are redefining machining capabilities. These advancements not only enhance the efficiency and accuracy of CNC lathe machines but also allow for greater adaptability in manufacturing processes. By 2025, the global CNC machine market is projected to reach $101.22 billion, and the introduction of multi-axis machining centers further exemplifies the industry's shift towards complexity and precision.
Moreover, the CNC plasma cutting machines market is expected to see significant growth, estimated to rise from USD 673.2 million in 2024 at a CAGR of over 5.1% until 2034. This trend is fueled by the increasing need for precise cutting solutions in various industrial applications. With the integration of AI driving this evolution, businesses can expect smarter machines that not only enhance productivity but also reduce operational costs. The Future of Machining report highlights these key trends, indicating a robust evolution in the CNC landscape as we approach 2025.
Evaluating Your Business Needs: How to Select the Right CNC Lathe for Your Applications
When selecting the right CNC lathe machine for your business, it's crucial to start with a thorough evaluation of your specific applications. According to a report by MarketsandMarkets, the global CNC lathe market is expected to reach $3.7 billion by 2025, driven by increasing demands for precision manufacturing across diverse industries. This statistic underscores the necessity of choosing a lathe that aligns with your operational needs, whether you're focused on high-volume production or specialized, intricate components.
Identify the materials you will be machining, as well as the complexity of your designs. For instance, industries utilizing titanium and aerospace-grade materials often require CNC lathes with advanced capabilities, such as multi-axis functionality. A recent study indicated that 70% of manufacturers report reduced cycle times and enhanced precision with multi-axis CNC lathes compared to traditional models. Thus, ensuring that the machine you select matches the intricacies of your projects can lead to significant improvements in efficiency and product quality. Properly assessing your business needs will not only aid in selecting the ideal CNC lathe but also contribute to the long-term success of your manufacturing processes.
Ultimate Guide to Selecting the Best CNC Lathe Machine for Your Business Needs
Feature | Importance Level | Recommended Specification | Typical Use Case |
---|---|---|---|
Maximum Swing Over Bed | High | 12 inches | Ideal for larger parts and complex geometries |
Maximum Length of Workpiece | Medium | 20 inches | Suitable for standard industrial components |
Spindle Power | High | 5 HP | Great for heavy cutting and high production |
Control Type | High | CNC Controller | Precision machining with automated settings |
Tooling System | Medium | Quick Change Tool Post | Enhances productivity with minimal downtime |
Cost Analysis: Budgeting for Your CNC Lathe Machine Investment and Future Upgrades
When selecting a CNC lathe machine, understanding the cost dynamics is crucial for effective budgeting and future upgrades. According to a report by Market Research Future, the global CNC machine market is expected to reach USD 100 billion by 2025, indicating a consistent demand for sophisticated equipment. For businesses looking to invest in CNC lathes, initial costs can range from $20,000 to over $500,000 depending on the machine's capabilities and features. Thus, it's essential to analyze both upfront and ongoing operational costs closely to ensure a sound investment.
Considering future upgrades is equally important as technology continually evolves. A study by TechNavio highlights that upgrading existing machines can increase productivity by up to 30%. Allocating 10-15% of your initial budget for upgrades can safeguard your investment and enhance your machine's longevity and efficiency. As a best practice, companies should also factor in training costs and maintenance when budgeting for CNC lathes, anticipating that proper training can reduce operational errors by approximately 25%, leading to a more effective use of resources over time. Proper financial planning ensures that your CNC investment remains competitive and adaptable to changing market demands.
Maintenance and Support: Ensuring Longevity and Reliability for Your CNC Lathe Machine
When investing in a CNC lathe machine, maintenance and support are crucial factors that can significantly extend the lifespan and reliability of your equipment. Regular maintenance routines, such as cleaning, lubrication, and inspection of moving parts, help prevent wear and tear. Establishing a proactive maintenance schedule tailored to your machine's specific needs can identify potential issues before they escalate into costly repairs, ensuring consistent performance in your production process.
Beyond routine maintenance, a reliable support system from the manufacturer or supplier is equally vital. Having access to knowledgeable technicians for troubleshooting, repairs, and replacement parts can minimize downtime and keep your operations running smoothly. Moreover, investing in training for your staff on proper machine handling and maintenance techniques can enhance your lathe's longevity. When selecting a CNC lathe, consider the availability of support services, including warranties and customer assistance, as these elements are key to sustaining productivity and saving on long-term operational costs.